- 過剰在庫
- 納期遅れの多発
- 遅れていることに気付けない
- 現場の現実と計画の乖離
- 立案スキルの継承が困難
- 謎の在庫品が増える一方
- 無駄な手待ちが多い
- 突発的なトラブルや欠勤に適切に対応できない
- 納期回答に時間がかかる
- 前工程の状況が見えない
- 試しに導入してみた生産スケジューラが使い物にならない
- せっかく立案したのに計画が無視される
- 製造現場全体の状況を把握できない
- 人や設備を増やしたらどうなるかわからない
- 営業と製造現場の板挟みが辛い
- 人員をうまく適材適所に配分できない
- 他の計画立案担当者とうまく連携できない
- 作業場所が見つからず計画どおりに着手できない
- モノが多すぎて作業場が足りない
- 生産管理システムの作業指示があてにならない
- あちらを立てればこちらが立たない
- 関係各所とコミュニケーションをとる余裕が無い
- 材料の欠品が多くてすべてが後手後手に回る
- 休日出勤して計画立案
- 急な注文、納期や数量の変更への対応が大変
- 生産性が上がらず利益が出せない
- 現場判断に任せざるを得ない
- 工場のキャパシティを超える生産要求に抗えない
- 必要な時にモノが揃わない
- 残業しないと生産が追いつかない
- 設備の制約条件が複雑すぎてよくわらない
解説:製造業の悩みを解きほぐす
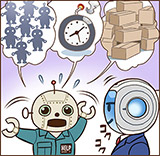
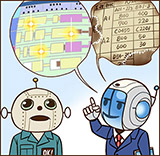
製造現場には無数の問題が噴出しますが、モグラたたきのように、それらのひとつひとつに振り回されて対処してもきりがありません。実はそれらの問題を整理していくと、本質的にはいくつかの課題に集約されることが分かってきます。
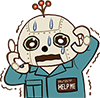
努力して計画を立てても、計画の変更が求められれば更新しなくてはなりません。手作業である限りはミスも発生しますし、確認作業の手間も馬鹿になりません。計画の内容が緻密であればあるほど、作業量はさらに莫大になります。逆に変更の影響が少なく更新作業を最小限に抑えられているとすれば、それは計画がおおざっぱであったり余裕を無駄に確保していたりするということの裏返しであり、工場の能力を十分に発揮できていないのかもしれません。
飛び込み注文、数量や納期の変更、作業員の急な欠勤や機械のメンテナンスなど、計画変更の要因は無数にあり、頻繁に発生します。これらに対応せず放置しておくと計画の信頼性はどんどん下がりますが、そのたびに計画担当者が計画更新という機械的な作業に従事していては、各部署との調整作業や情報収集などといった本来行うべきより重要な仕事がおろそかになってしまうでしょう。
このような定型的な作業をコンピュータに任せられるのであれば任せてしまうというのは、当然の判断といえます。コンピュータを利用することで無用なヒューマンエラーも回避できます。
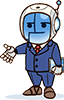
生産スケジューラFLEXSCHEは、緻密で正確な計画立案処理を高速に行うパッケージソフトウェアです。必要なマスターデータを事前に用意しておけば、オーダーや在庫などの条件を与えてリスケジュールするだけで、手間をかけずに計画を何度でも更新することができます。計画立案担当者が計画更新作業に費やしていた時間を、もっと有意義な業務に振り向けることができるでしょう。
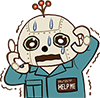
精度が低い
従来の製造計画立案手法の多くは、実際の各工程の作業や搬送に要する正味時間ではなく、ざっくりとした「標準リードタイム」に頼ったものでしょう。生産管理システム上でMRPに基づいて立案している場合もこれに含まれます。これは、1週間や1日といった時間枠(タイムバケット)単位での生産数量やリソースの負荷を見積もって、その期間にどのくらいの作業を詰め込めむかをざっくりと決めてやるものです。大量生産ならばこの手法でも通用するかもしれませんが、複雑な多品種少量生産では計画の精度を著しく損なってしまいます。また工程数が多くなると、製造に着手してから製品が出来上がるまでの時間(生産リードタイム)が本来の正味時間の何倍にも膨らんでしまい、それによる損失は計り知れません。
段取り(各作業のための準備や後始末)の発生条件が複雑であると総作業時間を妥当に見積もることが困難です。また作業中に使われる副資源(作業に従事する人、ツール類、電力など)の制約があると、実行可能な計画を適切に立案がそもそもできないこともあります。とりあえずおおまかな計画を押し込んで、あとは製造現場でなんとか対応(残業など)してもらうという乱暴な考え方は、今の時代には受け入れられなくなっています。だからといって、実行可能性を確保するために大きな余裕を与えてスループット(工場の生産性)を削るのでは本末転倒でしょう。
無駄が無く、かつ実行可能な計画を立案するためには、資源(製造に携わる設備、機械、人など)と品目の組み合わせごとの処理能力に基づいて妥当な作業時間を算出し、さまざまな制約に基づいて各作業の開始日時と終了日時を詳細に決めてやるしかありません。これが生産スケジューリング手法です。
従来の手法であれば、あるタイムバケット内で計画された作業が実際にその期間内のどこで実行するのかは計画段階では確定しないため、その次工程作業は次のタイムバケット(翌週や翌日)に行うことになり、生産リードタイムが大幅に間延びする原因になっていました。しかし詳細な日時が決まることにより、作業が午前中に終わればその日の午後には次工程に着手することができるでしょう。この手法であれば原理的には生産リードタイムを大幅に短縮することが出来るので、短納期化することができます。納期に間に合うように各工程を正確に見積もることで、予想外の納期遅れを防ぐこともできます。工場運営が劇的に変わります。
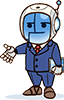
生産スケジューラFLEXSCHEは、ひとつひとつの実作業時間を秒単位で表現し、工場内での工程の流れを直接的にシミュレーションします。ある工程の終了後に所定の時間をかけて搬送すれば、すぐに次の工程に着手することができます。FLEXSCHEを使い始めれば、これまでの標準リードタイムやタイムバケットに基づく計画立案がいかに不合理であり、時間的にもコスト的にも大きな損失を引き起こしていたかを実感することでしょう。製造リードタイムの劇的な短縮が期待でき、受注量の変動に伴うゆらぎにも強くなります。
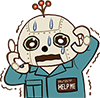
特定の人に依存している
工場には「計画立案の達人」がいて、たとえ複雑な制約条件や特殊な事情があってもその人に任せれば製造現場が回るけれども、他の人がやってもなかなか同じようにはできない、ということがしばしばあります。達人が長年の経験で蓄積したノウハウは得てして明文化・データ化されていないために後継者へ伝授が難しい場合も多いようです。またそもそも達人が立案した計画が本当に優れたものであるかどうか、第三者による検証ができていないことも珍しくありません。
この「属人性」の最大の問題は、達人の病欠や定年退職などのリスクです。そのようなリスクを自覚しながらも抜本的な解決策を見いだせていない製造業は決して少なくはないでしょう。その状態から脱却するためには
・雑多な制約条件や資源の能力
・工場の特殊な事情
・良い計画を立てるためのノウハウ
などを客観的にデータ化して、定型的な立案プロセスを確立することが必要です。
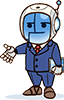
計画立案スキルの属人性は、どの工場でも大きな悩みの種になっています。だからといって、そのスキルをマニュアル化したり客観的なデータ化をしたりといった作業の負担が大きいわりには適切な手法も確立されておらず、二の足を踏んでしまうのも当然のことです。生産スケジューラFLEXSCHEの導入は、重要なきっかけを与えてくれるでしょう。「達人」の知識とノウハウを、FLEXSCHEのデータモデルとスケジューリングルールという表現形式で記述することで、次の世代への継承が大きく前進します。スケジューリング処理を実行するだけで、「達人」の立案の大部分を再現できるようになります。さらにスケジューリングの結果は瞬時に視覚化され、さまざまな観点から客観的に評価できるので、その妥当性を誰でも検証することができるのです。
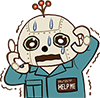
計画にフィードバックされない
せっかく計画立案して作業指図を製造現場へ送っても、実際にはどのように作業したか、つまり作業実績を次の計画立案に反映させなければ、計画と現実とのギャップは広がるばかりです。現実には完全に計画通りに作業ができるということはまず無いので、作業実績のフィードバックすることは正しい計画を立てるためにはとても重要です。それを怠ると、前回指示した作業がまだ残っているために新しい計画の実行に着手できなかったり、やることがなくて無駄な空き時間ができてしまったり、効率の良い作業指図を発行できなかったりするでしょう。
作業実績を何かしらの形で収集している製造業は少なくありませんが、その多くは業務分析や原価計算に利用するだけで、計画立案の質の向上のためにしっかり活用できている工場はまだそれほど多くないようです。なお作業実績を製造現場全体でリアルタイムに共有することで、スムースな計画遂行にも寄与します(後述)。
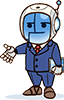
作業実績情報を生産スケジューラFLEXSCHEに取り込むことで、計画(=仮想的な工場)と製造現場(=現実の工場)の間が同期し、乖離を防ぐことができます。作業実績情報を制約条件として追加することで、次回の計画立案の精度が向上するのです。
作業実績情報には、ピンからキリまでさまざまなレベルの精度がありえます。各作業の開始日時と終了日時を正確に把握することもあれば、その日に行った作業を列挙するだけのこともあるでしょう。実績の精度は計画の精度に反映されますが、大切なのは、どんな精度であれ実績情報をFLEXSCHEにフィードバックして計画と現場の乖離を許さないことです。
さらに後述のFLEXSCHE CarryOut(フレクシェ・キャリーアウト)では、高精度の実績情報を製造現場で共有することで、計画精度の向上だけでなく、計画のスムースな遂行を実現します。
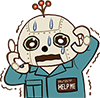
製造現場に作業指示を送るだけで、スムースに計画を遂行できるわけではありません。製造現場では、作業時間のゆらぎ、さまざまなトラブル、急な割込みの作業などといった変動要因はつきものです、変動が生じたときはリアルタイムに適切な対処が求められます。計画遂行は計画立案に劣らないくらい悩ましく難しい課題でしょう。
複数工程からなる製造現場では、前工程の進捗状況がその後の工程に大きな影響を与えます。仕掛在庫の増大やリードタイムの増加を犠牲にして工程間に十分な余裕時間を設けない限りは影響は連鎖しまうので、適切な対処が求められます。例えば前工程からの物品が搬送されてこないことで初めて前工程の遅れを知るようでは、対処が後手後手にまわってしまい、大きな無駄が生じます。前工程に着手した時点で遅れていること、あるいは予定より作業のペースが遅いことが分かった時点で、後工程にアラーム通知することができれば、より適切に対処するチャンスが得られるでしょう。
また班長など、立場によっては全体の進捗やトラブルなどの状況を把握しながら意思決定を随時していかなくてはならないこともあるでしょう。その決定された意志は新たな計画として製造現場全体で共有されなくてはなりません。
各工程では進捗状況を適切なタイミングで入力し、それはリアルタイムで共有されるだけでなく、作業実績情報として次の計画立案へのフィードバックに利用されるべきものです。
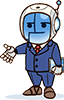
計画遂行を支援するシステムFLEXSCHE CarryOut(フレクシェ・キャリーアウト)を利用すると、その日の計画の複製を保持するサーバーから、製造現場の端末(iPad/Android/Windows)に工程・資源ごとの計画が配信されます。入力された作業の状況(開始や完了など)は製造現場全体で共有されるので、影響を受ける人は適切に対処することができます。サーバー上で局所的にスケジューリングすることで、現状に応じて計画を更新することもできます。製造現場の揺らぎの結果は、あるタイミング(1日の最後など)で計画立案者のスケジュールに実績情報としてマージされるので、翌日も精度の高い計画を発行することができるでしょう。